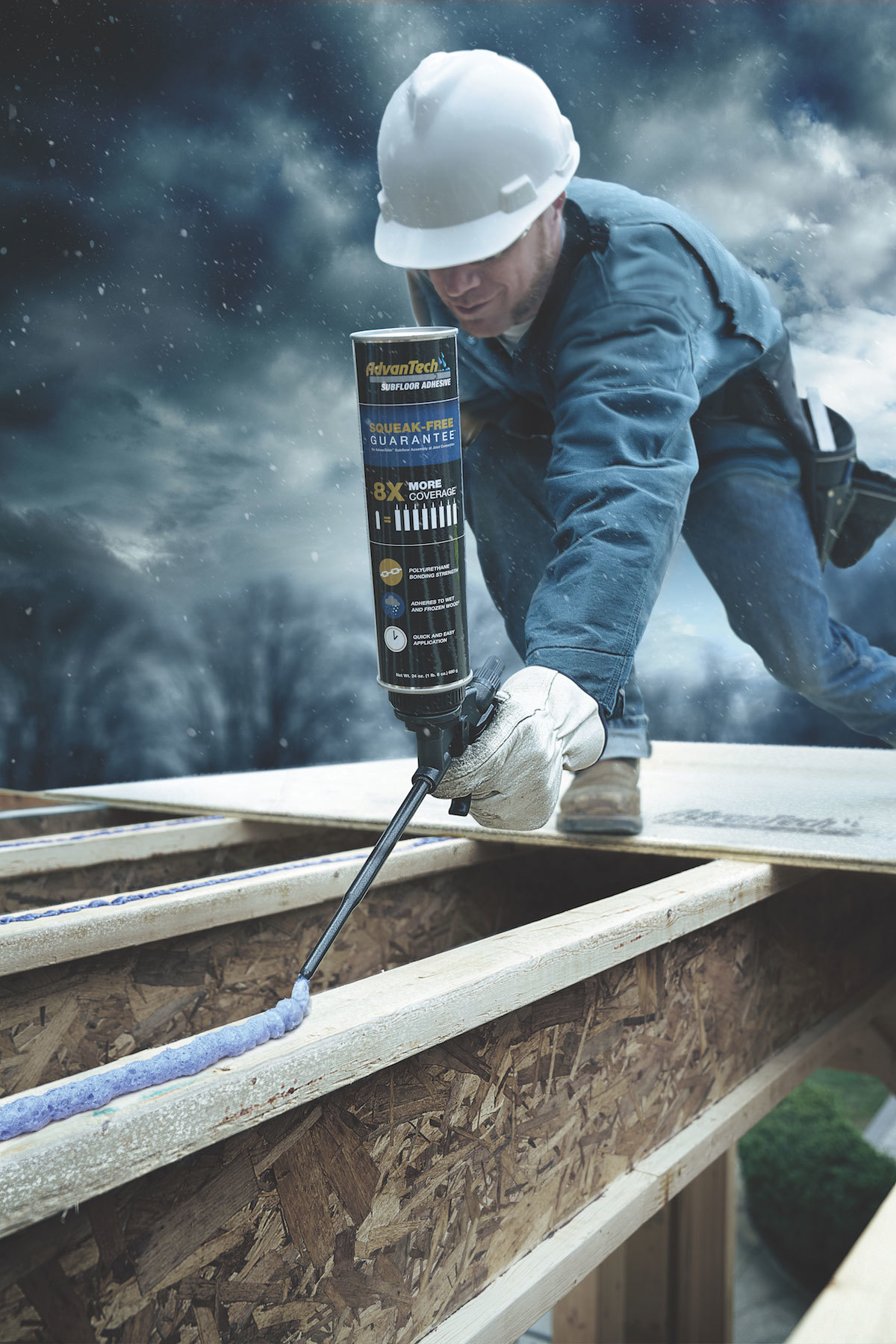
What to Do With Wet and Frozen Subflooring
3 Min Read April 25, 2018
With home building, overcoming the elements is a normal part of the job. In the winter months, cold air is nothing in comparison to the snow and ice on a jobsite. And, in the spring, the rainy season makes it particularly challenging to protect exposed materials. Here are a few tips for managing inclement conditions when your subflooring is exposed to wet weather.
How to Combat Snow and Ice
When building with AdvanTech® subflooring, avoid solid or liquid forms of salt. While these are good for melting snow and ice, they can open the surface of AdvanTech subflooring panels and let water into the wood pores. Remove ice and snow with methods that won’t affect the structural integrity of the panels.
- Dark, coarse sand absorbs heat from the sun, helps with the melting process and makes it safer to walk across the floor without slipping. It can be purchased at a local big-box or hardware store.
- Safe Paw Ice Melt is made with a glycol that can be applied before, during and after a winter storm.
- Bare Ground Liquid Ice Melt is more time-sensitive. It should be applied one to two hours before a storm and the temperature must be below 35 degrees. It comes in gallon containers and can be applied with a garden sprayer.
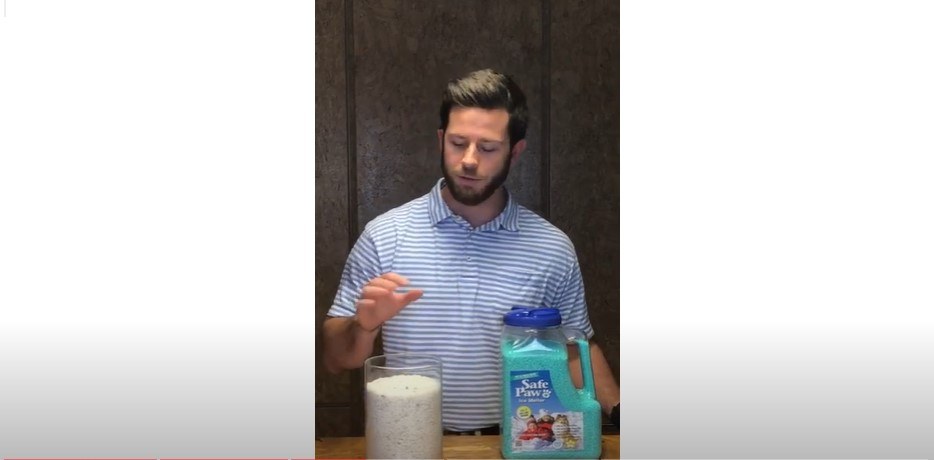
Your Subfloor Will Get Wet - How to Combat Water
Heavy rainfall can lead to standing water on the floor deck. While AdvanTech subflooring is engineered to withstand extensive water exposure with a 500-day No Sanding Guarantee,¹ you can take extra measures to protect your material if prolonged frozen, wet or dry cycles are anticipated when the wall framing isn’t up yet.
If it’s too late for rain preparation, there are a couple of water removal options. For standing water, wet vacuuming and sweeping are the best methods. Keep in mind that sweeping may be more difficult if the wall framing is up, so wet vacuuming could be easier.
Even when using a highly moisture-resistant subflooring like AdvanTech subflooring, allow panels to dry completely before installing finished flooring.
Not All Subflooring Is Created Equally
Unlike traditional commodity OSB products that can swell or delaminate, AdvanTech subflooring is engineered with a unique resin formula and process. This allows AdvanTech subflooring panels to not only stand up to snow, ice, and rain without flaking or swelling but also to maintain their strength and stiffness.
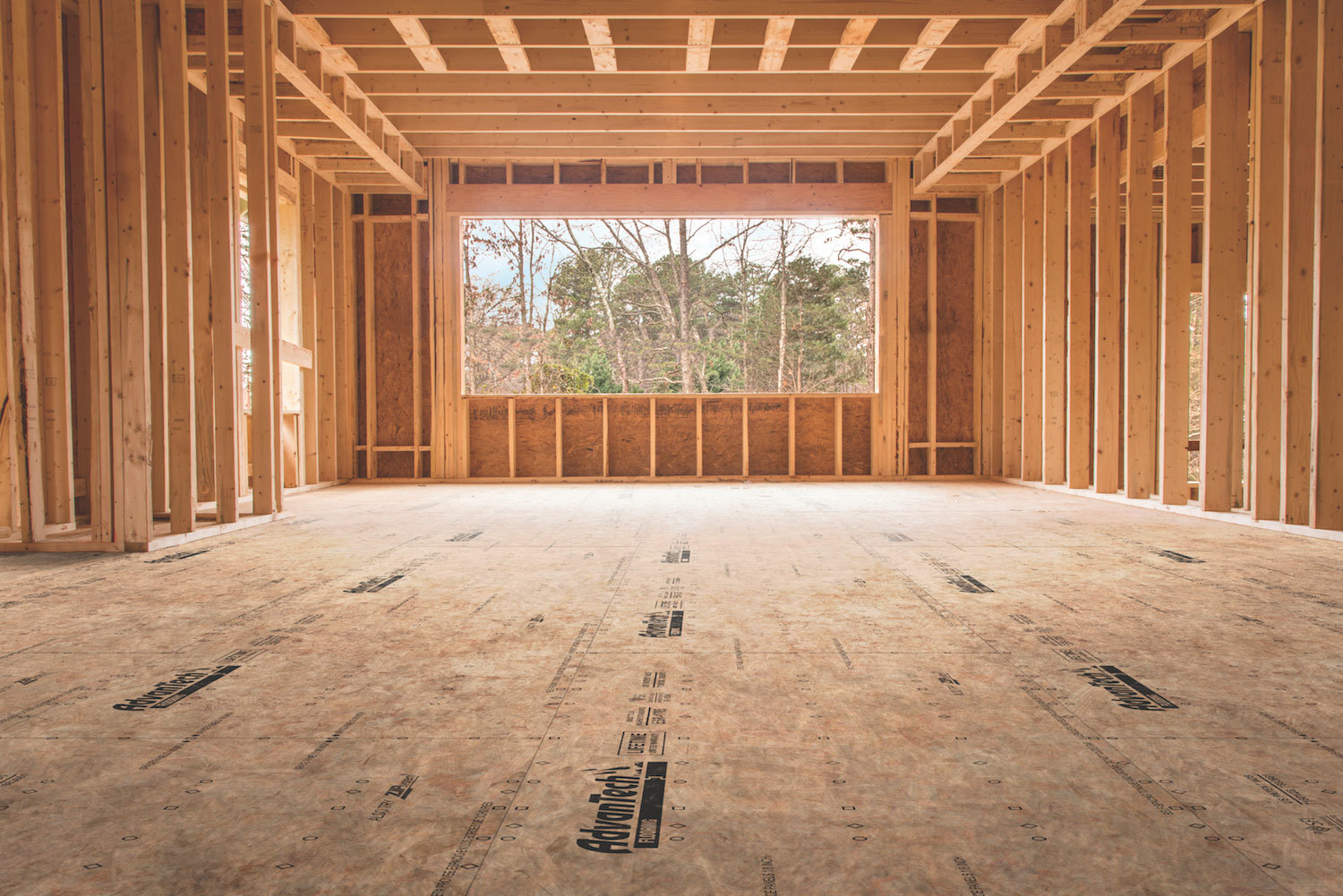
Strong Bonds in Wet and Frozen Conditions
When tackling a frosty, wet jobsite, keep in mind AdvanTech™ subfloor adhesive is a moisture-curing polyurethane adhesive. It not only provides a stronger bond than industry standards2 even in wet or frozen conditions, but it also applies easily with a gun-applied, foam-to-gel application—so no squeezing frozen cartridges!
With this easy-to-apply, strong panel-to-joist connection, AdvanTech subfloor adhesive used with AdvanTech® panels provide the right moisture-resistance and strength and stiffness, even under tough winter conditions. This combination helps you to achieve our Squeak-Free Guarantee3 and avoid warping, buckling, and bounce.
Learn more at AdvanTechAGame.com, or contact the technical support team for additional advice on using AdvanTech subflooring or ZIP System™ building enclosures products.
¹ Limitations and restrictions apply. Visit HuberWood.com/AdvanTech/ResidentialWarranty to learn more.
² Exceeds ASTM D3498 standard specification for field-gluing plywood to lumber framing for floor systems, dry, wet, frozen and gap-filling adhesion tests.
3 Limitations and restrictions apply. Visit 10-Year Squeak-Free Limited Warranty on AdvanTech™ Subfloor Assembly for more information.